石油行业储油罐资源整合困境探析技术瓶颈与运营挑战双重制约
石油行业储油罐资源整合困境:技术瓶颈与运营挑战的双重制约
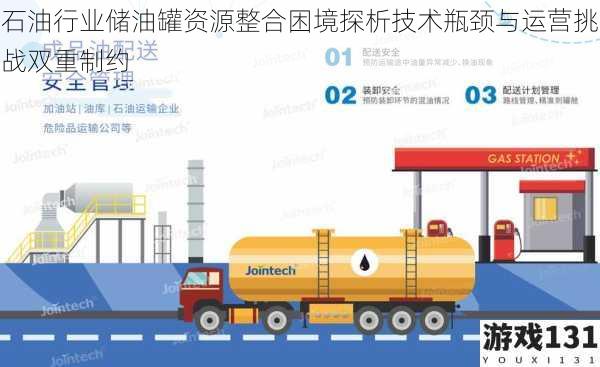
在全球能源转型背景下,石油行业储运设施的优化配置已成为提升产业竞争力的关键环节。我国作为全球第二大原油消费国,现有各类储油罐总容量超过8亿立方米,但资源整合率不足45%,远低于欧美成熟市场70%的水平。这种结构性矛盾既暴露了深层次的技术瓶颈,也反映出运营管理体系的系统性缺陷。
技术瓶颈形成的物理制约
储罐本体材料与工艺的适配性缺陷,构成了资源整合的首道技术屏障。我国现役储罐中,碳钢储罐占比达82%,这类材料在储存高硫原油时,罐体腐蚀速率最高可达0.8mm/年,导致储罐平均使用寿命较国际标准缩短5-8年。某石化企业2018年改造项目显示,将12万方储罐群整合为50万方级油库时,因材质差异导致37%的储罐无法满足新介质存储要求。
监测技术的滞后性严重制约动态整合能力。传统人工巡检模式下,储罐群安全监测周期长达72小时,无法满足现代化油库实时监控需求。2021年山东某油库事故调查显示,事故储罐在破裂前3小时已出现0.05mm的微裂纹,但既有检测手段未能及时预警。当前仅有14%的储罐装备了光纤传感系统,声发射检测等先进技术的应用率不足5%。
智能化升级面临数据孤岛困境。不同建设年代的储罐群存在自动化标准差异,某沿海油库整合案例中,新接入的2010年前建成的储罐群,其DCS系统与现有SCADA平台的协议兼容率仅为68%,数据采集完整度下降导致运营效率损失19%。
运营体系衍生的管理壁垒
多头管理架构导致协同效率低下。我国储罐资源分散在炼化企业、贸易商、终端销售等17类主体手中,中石化某区域公司统计显示,其管理的327座储罐涉及9个管理主体,标准化作业流程执行偏差率达43%。这种碎片化管理模式使得储罐周转率长期徘徊在0.8-1.2次/月的低水平。
技术标准体系不统一形成整合障碍。不同企业执行的储罐建设标准存在23项技术参数差异,包括焊缝检测标准、防火堤间距等关键指标。在长三角某储运枢纽建设项目中,因防雷接地标准不统一,导致12座10万方储罐的并网运营延迟11个月。
安全环保压力陡增运营成本。新安全生产法实施后,储罐区VOCs治理设施改造使单罐运营成本增加18-25万元/年。某央企测算显示,将三类不同标准的储罐群整合为智能化油库,安全环保投入占总改造成本的61%,投资回收期延长至9.7年。
破局路径与行业趋势
技术创新层面,新型储罐材料的研发已取得突破。某科研机构开发的纳米改性钢板,在同等工况下将腐蚀速率降低至0.12mm/年,材料寿命延长至40年。智能化监测领域,基于数字孪生技术的储罐健康管理系统可实现0.01mm级缺陷识别,预警响应时间缩短至15分钟。
管理优化方面,行业正在推进储罐技术标准统一化进程。新版石油库设计规范将储罐间距、消防系统等38项关键参数纳入强制性标准体系。某省试点项目通过建立储罐设施共享平台,使区域储罐利用率提升至78%,周转次数达到2.4次/月。
政策引导层面,国家能源局在"十四五"现代能源体系规划中明确提出,2025年前要建成10个国家级石油储备基地,推动建立储运设施共享机制。混合所有制改革在储运领域深化,某民营资本参与的储罐整合项目,通过技术托管模式使运营成本降低31%。
储油罐资源整合既是技术攻坚的战场,更是管理创新的试验田。在双碳目标驱动下,行业需要建立涵盖材料科学、智能监测、标准化管理和政策创新的系统性解决方案。只有突破技术可行性与经济合理性的平衡点,才能实现储运设施从物理聚合到价值创造的质变,为能源安全保障提供坚实基础。