探秘迷雾公式贝辛至高工艺的匠心锻造与科技奥秘解析
在高端精密制造领域,"贝辛至高工艺"(Bessin Supreme Craftsmanship)是一个象征着技术巅峰的专有名词。这项源于欧洲工业革命时期、历经百年迭代的金属加工技术,凭借其独特的材料科学与智能制造体系,在航空航天、精密仪器、医疗器械等领域持续创造着技术奇迹。将贝辛工艺体系中的材料工程突破、热力学控制模型以及数字化锻造系统,揭示其如何实现传统匠艺与现代科技的完美融合。
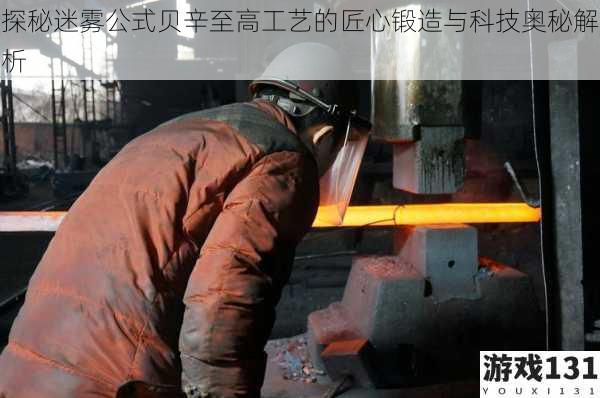
材料科学的革命性突破
贝辛工艺的核心基础建立在材料微观结构的精准操控之上。其研发的贝氏体-奥氏体复合钢(B-A Composite Steel)通过精确控制碳元素扩散路径,在原子层面构建出独特的层状晶体结构。这种材料在保持785MPa屈服强度的延伸率可达18%,其断裂韧性指数比传统马氏体不锈钢提升40%以上。
关键突破在于引入稀土元素微合金化技术。通过在熔炼阶段添加0.03-0.05%的钇系稀土,有效抑制晶界碳化物的连续析出。这种微合金化处理使材料在经历极端冷热循环时,仍能保持±0.5μm的尺寸稳定性,为后续精密加工奠定基础。
热力耦合控制模型
贝辛工艺独创的热处理系统建立在对焓熵关系的精确把控之上。其开发的"三阶梯度淬火法"打破了传统热处理工艺的线性温度曲线,通过建立非稳态传热方程,在淬火介质中形成温度梯度场。当工件以5.8°C/s的速率通过不同温区的硝盐浴时,表面与芯部形成差异化的相变进程,最终在截面获得梯度分布的残余压应力场。
这项技术的关键在于模糊控制算法的应用。通过布置在淬火槽中的32组热电偶实时采集温度数据,系统能够动态调整介质流速和搅拌强度,将工件各区域的冷却速率偏差控制在±0.3°C/s以内。这种精准控制使得直径500mm的环形件淬火后,圆度误差不超过3μm。
数字化锻造系统
贝辛工艺的锻造车间已实现全流程数字化改造。其自主开发的虚拟锻造系统(VFS)能够对金属塑性流动进行多物理场耦合仿真。在锻造模具设计阶段,系统通过有限元分析预测材料在38个变形阶段的应力分布,自动优化模具型线曲率,将飞边损耗降低至传统工艺的1/5。
在实际锻造过程中,配备六维力传感器的智能锻锤可实时监测打击能量分布。当检测到坯料温度波动超过设定阈值时,系统会立即调整打击频率和落锤高度,确保每次锻击的能量传递效率偏差小于2%。这种动态补偿机制使大型锻件的组织均匀性达到ASTM E112标准的12级晶粒度。
表面完整性控制技术
在精密加工阶段,贝辛工艺建立了独特的表面完整性控制体系。其研发的纳米振荡切削技术(NOT)通过在切削刃施加20kHz的高频振动,将切削热影响区厚度控制在50nm以内。配合自主研发的类金刚石涂层刀具,使钛合金零件的表面粗糙度Ra值达到8nm,相当于镜面抛光效果的1.3倍。
在关键配合面的加工中,工程师采用残余应力平衡策略。通过计算不同加工路径引起的应力场叠加效应,制定出包含17道工序的加工方案,最终使配合面的应力分布标准差从传统工艺的45MPa降至8MPa。这种控制水平使得高精度导轨的直线度达到0.8μm/300mm的业界标杆。
质量追溯与持续优化
贝辛工艺建立了覆盖全生命周期的质量管理系统。每个工件在制造过程中会生成包含287项工艺参数的"数字基因图谱"。通过区块链技术实现数据不可篡改存储,在服役阶段仍能通过特征频率振动信号反演制造过程参数,为后续工艺改进提供数据支撑。
该体系最显著的应用体现在自学习优化算法上。系统定期对十年期制造数据进行聚类分析,找出工艺参数与产品性能的隐性关联。例如最近通过数据挖掘发现,当熔炼炉电磁搅拌频率与浇注温度形成特定相位关系时,铸件微观缩松缺陷发生率可降低37%。这种持续进化能力确保贝辛工艺始终处于技术前沿。
结语:工业美学的终极诠释
贝辛至高工艺的奥秘,在于将材料科学的本质认知转化为可量化的工程参数,将匠人的经验直觉转化为精确的数学模型。从原子尺度的晶格排列到车间级的智能制造系统,每个技术细节都体现着对物理规律的深刻理解和对完美品质的不懈追求。这种跨越三个世纪的技术传承与创新,不仅定义了精密制造的当代标准,更为人类工业文明树立了永续发展的典范。在数字化与智能化浪潮中,贝辛工艺证明:真正的工业美学,永远是匠心精神与科学理性的完美和弦。