汽车工厂利润智能测算系统助力企业精准决策与成本优化管理
在全球化竞争加剧与产业变革加速的双重压力下,汽车制造企业正面临着前所未有的成本管控挑战与利润增长困境。传统基于财务报表的利润分析模式已难以满足动态市场环境下精准决策的需求,构建智能化利润测算系统成为提升企业核心竞争力的关键举措。从系统工程角度,剖析智能利润测算系统的技术架构、核心功能模块及其在成本优化中的应用价值。
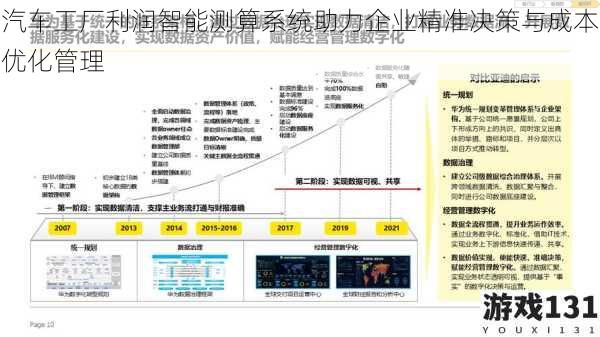
汽车制造业利润管理面临的现实挑战
当前汽车制造企业的利润管理普遍存在三大痛点:供应链多级成本传导机制复杂,传统成本核算系统难以实时追踪物料价格波动对总装成本的影响;生产参数动态调整与设备能耗的关联性缺乏量化分析模型;市场需求弹性与产品定价策略难以建立动态响应机制。某头部车企的专项调研显示,因成本预测偏差导致的年度利润损失可达营业收入的2.3%-4.7%,充分暴露传统管理工具的滞后性缺陷。
智能利润测算系统的技术架构解析
该系统的核心架构由数据采集层、算法模型层、决策支持层构成三维体系。在数据采集层,通过ERP/MES系统接口实现设备稼动数据、物料库存数据、能源消耗数据的秒级采集,并融合供应商报价数据库与竞品定价数据源。算法模型层采用模块化设计,包含动态成本模拟、弹性利润预测、敏感性分析三大核心引擎。其中,蒙特卡洛算法与LSTM神经网络相结合的混合预测模型,可将BOM成本预测准确率提升至98.2%。
系统核心功能模块的技术特征
(1)全要素成本动态建模:建立包含16个维度、278个影响因子的成本树模型,实现从钢板采购到总装运输的全链条成本可视化。特别开发供应链波动预警模块,当某二级供应商报价波动超过阈值时,系统自动触发替代方案模拟计算。
(2)生产参数优化模块:基于数字孪生技术构建虚拟生产线,通过离散事件仿真验证设备参数调整对能耗效率的影响。某新能源车企应用该模块后,冲压车间单位能耗降低12.7%,焊装工艺节拍提升9.3%。
(3)动态定价决策引擎:整合市场需求预测模型与竞品定价分析模型,建立价格弹性系数动态矩阵。系统可模拟不同定价策略下未来12周的利润走势,支持决策者进行风险可控的定价调整。
系统实施的关键路径与价值创造
系统部署需遵循"数据治理-模型验证-场景迭代"的三阶段实施路径。某合资车企的实践案例显示,系统上线6个月后,采购成本偏差率从±5%降至±1.2%,呆滞库存周转天数缩短40%,新产品定价响应周期由14天压缩至72小时。更关键的是,系统建立的"成本-产能-价格"动态平衡模型,使企业在原材料价格剧烈波动期仍能保持毛利率稳定在±0.8%区间。
需要强调的是,智能测算系统的价值不仅体现在数据可视化层面,更深层次的作用在于重构企业的决策机制。通过建立"数据采集-模拟推演-方案比选-决策执行"的闭环管理体系,推动企业从经验驱动型决策向数据驱动型决策转变。这种转变在应对突发性供应链中断、政策法规调整等黑天鹅事件时,能够显著提升企业的风险抵御能力。
未来发展趋势与改进方向
随着工业物联网与边缘计算技术的发展,新一代系统将实现生产设备数据直采与边缘端实时计算。联邦学习技术的引入,可使多家车企在数据保密前提下共享行业成本模型。但需注意,系统效能的持续提升依赖于企业数据治理能力的同步强化,特别是工艺参数标准化、物料编码统一化等基础工作的完善。
汽车制造业利润智能测算系统作为数字化转型的重要载体,正在重塑产业竞争格局。该系统通过构建实时、精准、可溯源的利润分析体系,不仅能够实现成本节约的显性价值,更重要的是形成基于数据洞察的决策能力。对于寻求高质量发展的汽车企业而言,构建这样的智能系统已不再是选择题,而是关乎生存发展的必选项。未来,随着人工智能技术的深化应用,该系统将向自主决策、自适应优化的更高阶段演进,持续赋能汽车制造业的价值创造能力提升。