机甲龙组装配置全流程详解:安装步骤与系统设置操作指南
机甲龙作为高精度仿生机械装置,其组装与配置需要严格遵循技术规范。将系统阐述从硬件安装到软件调试的全流程操作要点,确保设备达到最佳性能状态。
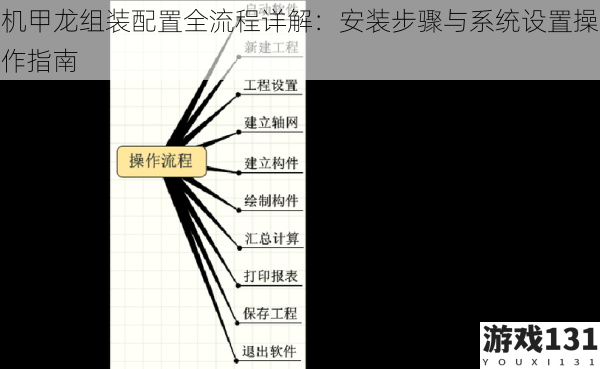
组装前准备
1. 工具与物料准备
需准备扭矩调节扳手(0.5-5N·m)、防静电镊子、精密螺丝刀套装(含PH000-PH2规格)、高温润滑脂及专用校准工具包。所有部件需按照部件清单进行三次交叉核验,重点检查伺服电机(型号DR-9X系列)编码器线缆完整性。
2. 工作环境设置
搭建防静电工作台(表面电阻10^6-10^9Ω),环境温度控制在22±3℃,湿度维持45%-60%。建议在操作区设置定向照明系统,确保关节轴承安装位的可视精度达到0.1mm级。
机械结构安装流程
1. 核心骨架组装
(1)从中央脊柱模块(部件编号AX-01)开始,采用交叉紧固法安装钛合金支撑架。使用2.5N·m扭矩扳手分三次旋紧M3×12沉头螺钉,每次增加0.8N·m,并在螺纹处涂抹微量螺纹胶(LOCTITE 243)。
(2)安装骨盆传动箱时,需同步校准X/Y轴定位销,插入阻力不应超过5N。建议使用激光定位仪辅助对中,偏差需控制在±0.05mm以内。
2. 关节系统配置
(1)四肢关节采用三自由度球铰结构,安装前需对NSK 6902ZZ轴承进行预润滑处理。注入润滑脂量应占轴承空隙的30%-35%,过量会导致运动阻力增加。
(2)膝关节安装需特别注意谐波减速器(型号HD-14-100)的相位对齐。使用专用校准夹具固定输入轴与柔轮,确保波形发生器标记线与刚轮基准线重合。
3. 外装甲装配
(1)采用模块化装甲板拼接技术,每块装甲(尺寸150×200mm)使用8个快拆锁扣固定。安装时应遵循"中心辐射"原则,从胸甲开始向外扩展。
(2)在尾椎部装甲装配时,需预留动态形变空间。相邻装甲板间隙应保持1.2-1.5mm,使用硅胶垫片进行缓冲隔离。
动力系统集成
1. 电机与传动装置
(1)伺服电机(功率300W)安装需使用热传导胶(TG-30M)填充电机座间隙,确保散热效率。动力线缆走线应避开运动轨迹区域,弯曲半径不小于线径的5倍。
(2)同步带传动系统张紧力需通过频率法校准。使用张力计测量固有频率,当1m长度带体振动频率达到120±5Hz时为最佳状态。
2. 液压辅助系统
安装微型液压缸(工作压力12MPa)时,需进行三次排气操作。每次加压至8MPa后开启泄压阀,直至油液流动无气泡产生。建议使用32#航空液压油,加注量不超过油窗的80%。
电子系统配置
1. 控制中枢安装
主控模块(型号CTL-X7)应安装在设备重心投影区,使用三轴加速度计验证安装平面度。数据总线采用星型拓扑结构,每条CAN总线长度不超过3m,终端电阻设为120Ω。
2. 传感器网络部署
(1)力反馈传感器(量程0-500N)安装在肢体末端执行器内部,信号线需做双层屏蔽处理。建议每通道采样率设置为2kHz,噪声水平控制在±0.5%FS以内。
(2)环境感知系统集成时,毫米波雷达(探测距离30m)与双目视觉模块需保持轴线平行度误差<0.1°,使用六点定位法进行空间标定。
系统初始化设置
1. 控制协议加载
通过JTAG接口烧录运动控制固件(版本需≥V2.18),首次启动时选择D-H参数建模方式。建议采用改进型Craig参数定义法,关节坐标系偏差补偿值不超过±0.03rad。
2. 伺服系统调参
(1)在PID参数整定界面,先设置Kp=0.5、Ki=0、Kd=0进行阶跃响应测试。逐步增加微分增益直至超调量<3%,积分时间常数建议设为速度环周期的1/2。
(2)进行全关节零位校准时,需先解除机械限位,使用绝对式编码器自动寻参功能。重复定位精度应达到±15角秒,否则需检查谐波减速器背隙。
3. 人机交互配置
(1)语音控制模块需采集操作者5组声纹样本,训练时长不少于30分钟。命令识别阈值设为-25dB,响应延迟控制在200ms以内。
(2)在HMI界面设置三级安全权限,工程师模式需双因子认证(密码+动态令牌)。紧急停止按钮回路应独立于主控系统,响应时间<50ms。
系统联调与验证
1. 运动性能测试
执行ISO 9283标准测试程序,重点验证:
2. 智能算法验证
(1)路径规划模块需通过迷宫测试,要求能自主生成8阶贝塞尔曲线轨迹。
(2)深度学习模型(YOLOv5架构)需达到97%以上的目标识别准确率,测试集应包含雨雾、低照度等复杂场景。
本流程严格遵循ASME B5.54标准,建议每运行200小时进行预防性维护。特别注意谐波减速器的2000小时润滑周期,以及光电编码器的定期清洁(使用无水乙醇棉签擦拭)。通过规范化操作,可确保机甲龙系统MTBF(平均无故障时间)达到5000小时以上。