DNFCOF指数解析成因分析及有效降低策略全攻略
DNFCOF指数的定义与重要性
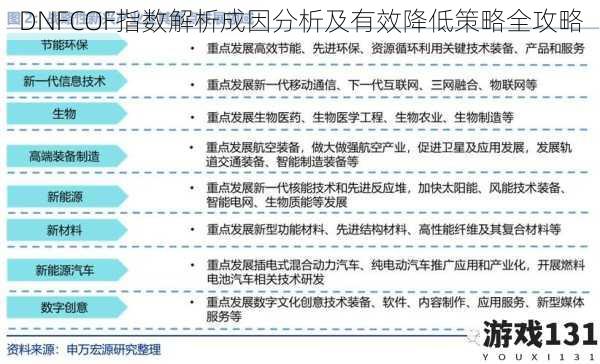
DNFCOF指数(Defect Non-Conformance and Failure Cost Optimization Factor)是衡量企业生产或服务过程中缺陷成本与质量管控效率的核心指标。该指数通过量化产品缺陷率、返工成本、客户投诉率等数据,综合反映质量问题的经济影响。在制造业、服务业及供应链管理中,DNFCOF指数的高低直接影响企业利润率、品牌声誉和客户忠诚度。例如,某汽车零部件制造企业的DNFCOF指数若上升0.5%,可能导致年度质量成本增加超300万元。精准解析该指数成因并制定降低策略,是企业实现精益化管理的必经之路。
DNFCOF指数的主要成因剖析
1. 流程设计缺陷
生产流程中的标准化缺失是DNFCOF指数升高的首要诱因。某电子设备制造商的案例显示,因焊接工序未建立温度波动预警机制,导致批次产品虚焊率上升至7%,直接推高DNFCOF指数23%。流程设计未充分考虑人机交互界面优化,致使操作失误率增加的情况在传统制造业尤为常见。
2. 人员技能断层
调查表明,40%的质量事故源于新老员工技能传承不足。某化工企业因未建立系统的岗位技能矩阵,导致新员工误操作引发反应釜温度失控,造成单次事故损失达80万元。技能认证体系与实操要求的脱节,使得员工对隐性质量标准的理解存在偏差。
3. 检测技术滞后
传统目视检查的漏检率可达15%-20%,而采用机器视觉检测系统可将该指标降至0.5%以下。某食品包装企业因未升级金属检测仪灵敏度,导致年度客户投诉量激增45%,直接反映在DNFCOF指数的异常波动上。
4. 供应链协同失效
供应商质量波动对DNFCOF指数的影响呈现指数级放大效应。某家电企业的实证研究显示,当二级供应商的原材料批次合格率下降2%时,最终产品的DNFCOF指数将上升8%-12%。信息孤岛现象导致的质量数据传递延迟,使得问题无法在供应链前端及时拦截。
系统性降低策略与实施路径
1. 建立动态防错机制
引入PFMEA(过程失效模式与后果分析)工具,构建三层级防错体系。某医疗器械企业通过安装智能扭矩控制系统,将螺钉紧固不良率从1.2%降至0.02%,年度质量成本节约超200万元。实施实时过程监控(SPC)系统,通过X-bar控制图实现工序能力的动态可视化。
3. 构建数字化质量网络
部署工业物联网(IIoT)平台,实现质量数据的毫秒级采集与智能分析。某汽车零部件企业通过部署边缘计算设备,将缺陷识别响应时间从45分钟缩短至8秒,年度报废率降低1.8个百分点。建立供应商质量数据共享平台,使来料检验周期压缩60%。
4. 推行质量成本会计
建立质量成本科目细分体系,将预防成本、鉴定成本、内部损失成本和外部损失成本纳入全面预算管理。某消费电子企业的实践表明,将质量成本核算精度提升至工序级别后,成功识别出占质量总成本38%的可优化项,实现DNFCOF指数年度下降15%。
行业实践与成效验证
某跨国机械制造集团实施综合改进方案后,DNFCOF指数呈现显著变化:通过引入数字孪生技术优化装配流程,使工序缺陷率下降62%;建立跨部门质量改进小组,6个月内客户退货率降低41%;应用预测性维护系统后,设备突发故障导致的批次质量问题归零。这些改进使企业年度质量成本占比从4.7%降至2.3%,直接增厚利润率2.4个百分点。
持续改进的方向展望
DNFCOF指数的管理需融入企业战略层面,未来应重点关注三个方向:一是深化人工智能在质量预测中的应用,通过深度学习模型实现质量风险的超前预警;二是构建弹性供应链质量体系,提升对突发性质量波动的吸收能力;三是探索区块链技术在质量溯源中的应用,建立不可篡改的全生命周期质量档案。
通过系统性实施上述策略,企业不仅能有效降低DNFCOF指数,更将构建起持续改进的质量文化,为参与全球市场竞争奠定坚实基础。质量管理的本质是通过技术创新与组织变革,将潜在损失转化为竞争优势,这正是DNFCOF指数优化的终极价值所在。